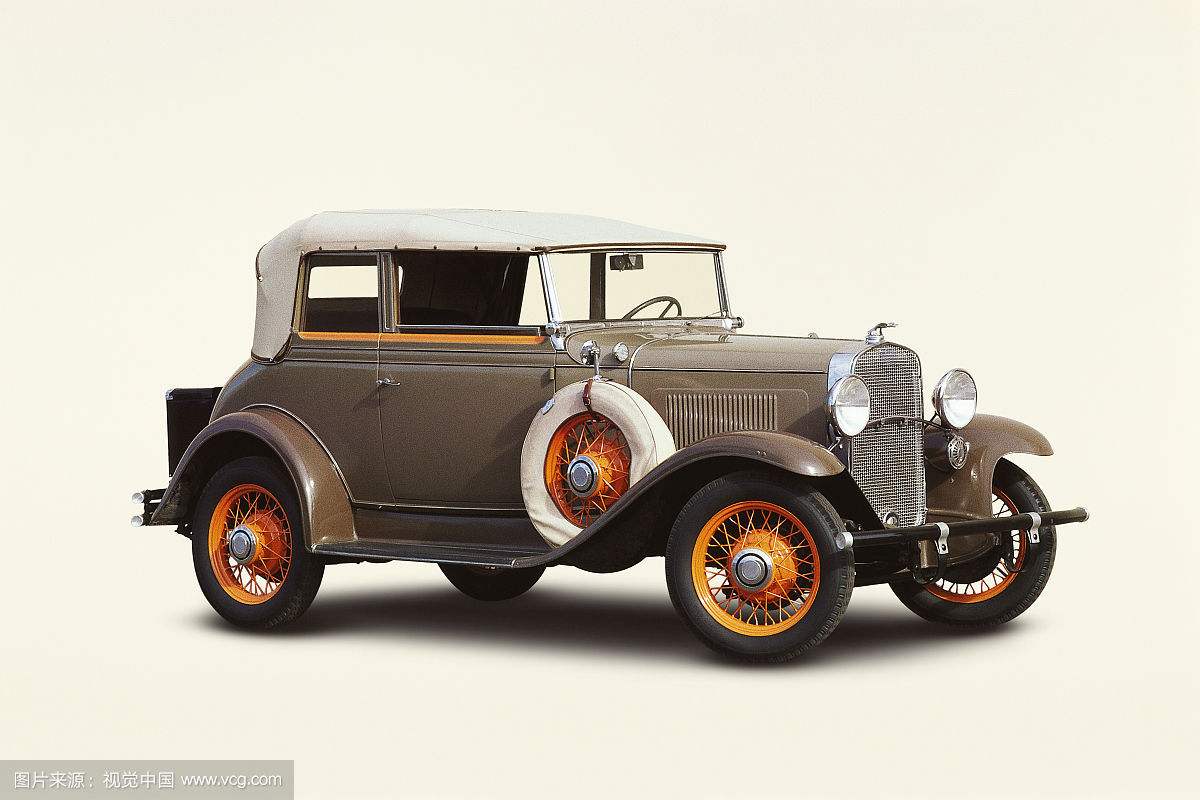
长安汽车UNI-T生产基地主要生产SUV、MPV等车型,生产线采用了先进的工艺和设备。冲压车间为全封闭高速双臂机械生产线,生产节拍达15次/分,低噪环保,同时采用同步控制,数控液压垫,全自动换模等关键技术。焊接首次采用4车型柔性线,自动化率达50%。涂装车间为水性3C1B+VOC末端焚烧工艺,采用底部挤胶、底部密封、喷涂机器人。总装车间采用可升降大滑板,智能适应作业高度,底盘自动合装AGV,玻璃自动挤胶、扭矩控制系统等。同时,以“时间更短、成本更低、库存更少、空间更小”的物流理念,着力打造成为一流的现代化工厂。
冲压车间
冲压车间总建筑面积25820㎡,有2条2400T双臂全自动高速封闭式冲压生产线,最高生产节拍达15(冲次数)/分钟,车间年最大产能达700万(冲次数),代表着当今国际最先进大型成套冲压设备生产水平。按照精益化、敏捷化、柔性化的生产理念,采用同步控制、全自动换模、节能型数控拉伸垫、全数字化监控等关键技术,主要承担长安汽车车型的大型外覆盖件冲压生产任务。
冲压生产线 是一条先进的智能化系统生产线,采用快速,高效的全自动换模系统,换模成功仅需要3分钟,提高了自动化线的生产效率及设备安全性,更加符合自动化线的柔性化生产要求,满足了现代化汽车,冲压工厂的实际生产需要。
全封闭式冲压 冲压车间采用先进的液压垫技术,板料成型过程可以对参数进行控制,保证了零件很好的成型和刚性硬朗。冲压车间采用全封闭式的大型冲压设备,防尘降噪可以有效的将噪音分贝降到国家标准85分贝以内。
行车吊具 在改良改善方面,车间员工充分运用自身的智慧和才能,充分利用现有资源,自行设计并制作行车吊具,安装在生产线行车上,减少了冲压生产线换模时间,按每年生产200天计算,一年可节省约200小时,极大的提高了换模效率,并降低了操作工人的劳动强度。
多功能立体仓库 冲压车间存放端拾器的多功能立体仓库,可实现端拾器出入库的管理自动化,数据维护查询、库存分析,打印报表等功能,可以在90秒以内完成端拾器的自动存取,节约面积达1800平方,符合现代化车间敏捷生产的要求。
焊接车间
焊接车间总占地面积为42000㎡,主要由一条柔性化主线和一条刚性主线和车身储运线构成,设计产能26万辆/年,最大产能为39万辆/年。为凸显智能焊接质量领先能力,车间配置具有国际化一流品质的全自动化设备336台。
白车身精度98.9% 自投产以来,批量质量事故发生为“0”,白车身精度截至目前已攀升至98.9%,在长安汽车各制造基地排名第一。
精度培育中心 它就像超大型的X光检测仪一样,通过2台悬臂式三坐标测量机(瑞士进口海克斯康三坐标仪,最大承载重量≥8000Kg,可以满足大型SUV,MPV测量需求;单臂模式空间测量精度MPEE≤70um,双臂模式空间测量精度MPEE≤90um)、2台高精度激光跟踪仪、12副门盖总成检具,2套PCF综合检具及1套开口检具,将整车焊接主拼过程中对零部件来料、工装夹具测试、模具精度和过程控制进行100%无死角全过程监控,针对异常开展逻辑性关联分析和数据整合,让白车身焊接过程产生的异常无所遁形,凡0.8-1.2mm公差范围内问题得到100%全部规避,白车身精度监控较常规提升50%。此类模式在全行业独树一帜,遥遥领先。
视觉检测系统 整车焊接最基础的下车体(底盘)自动生产线。为保证底盘密封效果,设计之初引进了产自德国的康耐视鹰眼 —— 视觉检测系统,对挤胶效果密闭性能能100%验证。验证充分之后,即进入右侧的工位抓取前壁板,通过EMS(输送系统)传输至下车体组拼连接。
焊点打点指示改善 由于后地板在焊接时覆盖其它小零件,存在大量视线盲区,只能凭感觉、经验盲焊,时常出现半点焊、焊伤零件情况,质量保证难度大。经过车间、班组不断验证,采用激光笔指示打点。确定激光笔安装位置后打点操作,既不影响焊钳进出,也不影响焊接操作,通过改善,大幅度减少焊伤产生机率,减少反复瞄准动作,单次操作缩短5秒,年节约返修工时费125857元。
自动化线机器人 配置了产自德国库卡的117台机器人,100%实现零部件自动焊接与抓取,能够在长安汽车各车型间快速实施全柔性化切换,工位间采用现今最为稳定和效率最高的高速滚床传输,传输时间≤4S,较传统传输效率提升200%以上,实现了定位精确、运行平顺、传送高效,在长安汽车各制造基地处于领先地位。
在线检测系统 这套系统来源于德国康耐视,目前在整车制造行业处于一流领先水平,是基于视觉检测和激光测量技术的在线非接触测量系统,突破传统三坐标抽样检测限制,可100%实现整车工艺尺寸波动监控,为工艺改进提供有效的数据支撑。 在这里,我们为确保100%无残次品流转至下工位,对固化VIN刻字压印效果也进行了改善,彻底改进由人工检查压印方式,在压印机器人增加光源与CCD高清摄像头(后期可与视觉检测系统连接),连接人工工位显示器,将实时压印效果传输在显示器。并在位作业指导书增加检查压印效果步骤,确保压印状态。通过改善年节约返修、能源费用117195元。
车门线 工艺布局经过与丰田、上海大众等国际、国内一流整车企业对标,采用分区对称布置,有效的规避了各品种车门库存居高不下的问题,场地占用缩减30%以上,物流配送时间缩短25%以上。在扣合过程中,我们采用四模倒库系统,实现挤胶、扣合全自动,并实现单台压机最短时间模具相互切换,可达成四种车型同步扣合,真正意义上实现全过程柔性焊接。
地板链调整线 这是国内同行业第一条节拍达成65JPH的地板链。在这里,上下车体合拼后会依次完成二氧化碳保护焊、高工位顶盖、五门一罩、白车身的调整。整个焊接工艺的使命已经圆满达成,这一台台完整的、无瑕疵的白车身正有序排列,进入涂装。
总装车间
长安汽车UNI-T生产基地总装车间,作为长安汽车面积最大的车间,车间总占地91500㎡,主要由9条主线、6条分装线、2条辅助输送线、2条检测线和2条淋雨线构成,设计产能26万辆/年,最大产能为39万辆/年。为彰显智能、数字化总装领先能力,车间配置具有国际化一流品质的全智能、自动化设备149台,占比达80%,实现生产、设备、质量和物流相互间的决策智能化监控和管理。生产效率提高15%以上、资源利用率提高10%以上、产品研制周期缩短25%以上、运营成本降低15%以上、产品不良品率降低25%以上、关键制造装备运行监控率达到100%,总装车间制造智能化出于同行业领先水平。
总装车间生产线 总装车间生产线设计节拍为65JPH。外观检查线,也就是总装车间主线末端,整车就是在这里经过五门调试、外观检查及汽油加注后下线。完成线共计2条,主要从事座椅、车门、正压检测、加注等工作。值得一提的是,四合一加注设备采用国内设计国外加工形式,加注精度可达95%,从而保证我们产品的加注质量。
车门合装工位 待车体从涂装进入总装到达生产线第一个工位时,便将车门拆掉,在车门分装线进行车门零部件装配,然后通过运输线直接达到此处,进行车门组装,这样的生产线设计极大程度上方便了车体内饰装配,节约32秒/车装配时间。
底盘线区域 共计两条线54个工位,主要从事发动机、后桥、油箱、轮胎、排气管等底盘零部件装配工作。在关重扭矩控制方面,共有75套扭矩控制设备,采用法国马头控制系统,确保扭矩合格率100%。在我们左侧是发动机和后桥的装配工位,目前我们采用的是新松双举升底盘合装大AGV,实现了发动机和后桥同时装配。
轮胎分装线区域 最快节拍12S完成一个轮胎分装,是目前国内自动化水平最高的轮胎分装线。轮胎分装线装配完成后,经过二层平台输送到达轮胎合装工位,并将输送到达的轮胎采用螺旋状设计下放至生产线,这样既保证了库存量也降低了我们在制造过程中对轮胎的磨损。
总装车间物流区域 车间物流区域面积11000㎡,按物流区域功能不同,划分为库存、打包、集中排序3大功能区,其中库存区以工艺路线、现场区域面积预留为基准,以配送距离近、物流路径单循环为原则进行“模块化”规划,规划托盘库位1537个、料架库位287个;打包区以MES系统为依托,引进Kitting拣料系统、AGC同步配送系统,对270类物料(单车型)打包,实现AGC单套物料智能化同步配送,智能化率达29%;集中排序区物料196类,采用电动拖车配送,同步化率达65%。
蓝鲸NE平台
UNI-T 搭载的蓝鲸NE1.5T 高压直喷发动机,源自中国首个模块化发动机开发平台——蓝鲸 NE 动力平台,是长安汽车集全球资源,基于领先的模块化顶层设计,历时 4 年打造的面向下一代排放、油耗法规标准的全新动力平台,设计覆盖 1.0-1.8L排量,全系兼容 48V、HEV/PHEV、REEV,通用化率高达98%,产线自动化率、智能化率达国际先进水平。蓝鲸NE 融汇一系列先进的发动机技术,具备净、劲、静三大强劲优势;同时,完成多达300 余项系统级、2000 余项零部件级的试验验证,性能出众,品质过硬。
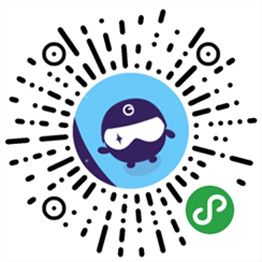
评论
() 先登录 发表暂无评论
点击展开更多评论