
“工人很少啊!”走进车间,很多人问出了这句话。“目前,全铝车身车间实现了100%自动化率,335台机器人都是来自ABB,瑞士制造中国组装。人工作业更多在质检。”领队的工程师介绍。
这是国内首家专制全铝车身车间,来自奇瑞捷豹路虎常熟工厂。工厂里面,整齐划一地停放着去年上市的两款车型——国产揽胜极光、国产发现神行。而2016年,来自捷豹品牌的XF加长版车型,将首次采用全铝车身亮相今年的北京车展,并于下半年完成国内量产、上市。
奇瑞捷豹路虎的“第二阶段”
2015年9月,奇瑞捷豹路虎经历了成立以来的高管调整。出身采购的百润与朱国华完成了奇瑞捷豹路虎公司研发、制造、采购、市场和人才体系的搭建,由技术派Murray Dietsch和陈雪峰分别接任奇瑞捷豹路虎公司总裁和常务副总裁。由此,奇瑞捷豹路虎第二阶段正式开展。
对于奇瑞与捷豹路虎的“联姻”,一直有对国产化后质量担忧的声音。2012年,投入10亿英镑后,路虎揽胜首次推出全铝单体,整体减重39%。而本次引入全铝车身技术,也许正是Murray在发布会上反复强调的“对于质量的提升”。
奇瑞捷豹路虎总裁Murray Dietsch
奇瑞捷豹路虎全铝车身车间占地48384平方米,除了采用先进的铝材技术,搭配而来的自冲铆接技术、胶合技术也是实现全铝车身满足轻量化与可靠性的必要手段。
捷豹品牌在铝合金技术的创新与积累上有着世界领先的优势。铝的优势在于轻巧、坚固、可回收,对优化重量分配有相当的帮助,可以“让”出更多的重量空间用来分配其他技术设备。奇瑞捷豹路虎表示,相比于传统车身平台,智能全铝车身架构具有模块化设计的优势。即将国产的捷豹XF长轴距版,铝合金应用比例已达75%,其中独家采用的RC5754高强度铝合金,由全球顶级铝材供应商诺贝丽斯定制化供应,应用于加强件;而AC300 T61 等高强度铝合金,则应用于碰撞结构中。
奇瑞捷豹路虎全铝车身骨架
全铝技术引进,国内首次揭秘
对于铝材在轻量化中的表现,一直受到各大汽车品牌的认可,但本次国内首次揭秘全铝车身车间所展示出的车身铆接胶合技术,还是引起了探访团队的诸多好奇。“铆接,而不是焊接,真的能保证强度吗?”
捷豹车身结构高级经理Simon Black称,这项铆接胶合技术,最早应用于航空领域。对于自冲铆接技术应用于汽车制造工艺,其实捷豹路虎从上世纪90年代起就已经开始了研发和尝试,有了比较多的经验积累。
从环保的角度而言,自冲铆接具有汽车制造行业车身连接工艺中非常低的能耗与污染。冷连接的技术不会让部件产生热变形、无飞溅物产生;为了保证铆接技术拥有更高的抗疲劳强度与静态紧固力,奇瑞捷豹路虎在车身上设计了2754个铆点,在整体铆接结束后,会针对强化部位进行补铆。
奇瑞捷豹路虎自冲铆接技术,全车身共有2754个铆点
为了保证车身强度,奇瑞捷豹路虎引入了一种特殊的黏合剂,在高温下,黏合剂硬化,可将车身强度增大至单纯铆接时的2-3倍。车身连接工艺中,铆接胶合技术占比72%,完成自冲铆接的机器人,则占据了车身车间机器人总数的70%,目前居国内同业之首。“这些是摄像,用来实时监测全铝车身的品质和数据。”对于质量保证体系,奇瑞捷豹路虎的工程师表示,工厂具有自冲铆接的实时过程监控、可视化涂胶监测系统、激光在线精度测量控制系统、铆接点的无损检测和破坏性测试等一系列流程。
奇瑞捷豹路虎全铝车间激光在线精度测量
对于工厂中的空地,工程师说,这是为了捷豹XF加长版量产后,预留的物流区域。“相信到时候会非常忙。”
作为首家中英合资的高端汽车企业,奇瑞捷豹路虎走过了三年的积淀期。奇瑞捷豹路虎常务副总裁、“技术范儿”的陈雪峰表示,对于汽车企业,显著减少工业碳排放是非常大的挑战。奇瑞捷豹路虎的可持续发展愿景是,既要满足消费者需求,也要迎接工业碳排放的挑战。国产捷豹XF长轴距版之后,奇瑞捷豹路虎将有更多节能、环保的产品在常熟工厂投产。
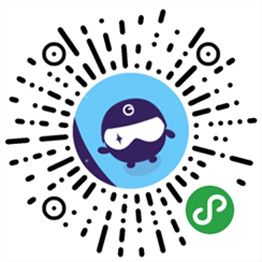
-
日前,我们从奇瑞官方获悉,奇瑞汽车将会在今年4月北京车展上带来5款新车,其中包括瑞虎7和3款新能源车型,以及1款品牌愿景概念车。其中,除艾瑞泽7 PHEV外均为首次亮相。转载 2016-03-31
-
首先,我个人觉得奇瑞山寨国外的豪车品牌,现阶段倒是可以理解。孙思聪 2016-03-21
-
路虎官方宣布第四代发现新车型正式上市。新车共计四款车型,售价区间为82.80-104.80万元。转载 2016-04-07
-
高德车载导航输出的多种信息,可以在捷豹XJ车型前装的四块屏幕上进行分布显示、协同交互。转载 2016-03-24
-
现在的汽车行业,尤其是在互联网和汽车的发生深刻交互的时间节点,大家能感受到的关键词就是“变化”——整个汽车产业从生产到销售的各个环节,甚至后市场方面都在发生深刻的变化。转载 2016-03-24
-
位于索利赫尔的路虎是英国汽车的骄傲,有着悠久的历史和深厚的底蕴,而二十多年前诞生的路虎发现系列进一步丰富了路虎的越野文化,为路虎日后的发展做出了不可磨灭的贡献,其魅力更是经久不衰。下面让我们翻开历史,阅览路虎发现系列的过去。闫方承 2015-12-03
评论
() 先登录 发表暂无评论
点击展开更多评论